Bosch Rexroth Offers Complete Factory Automation Solutions
The Bosch Rexroth team discussed the launch of ctrlX I/O which adds other interfaces on the field and control levels to the ctrlX AUTOMATION platform. The I/O range facilitates horizontal and vertical integration on the one hand and serves as a functional expansion of the control platform ctrlX CORE on the other. In the future, comprehensive communication and performance enhancements as well as I/O modules geared to technologies of the future like 5G, TSN and AI will be offered. The new comprehensive automation solution will create a broad range of connectivity and networking options in the increasingly digitalized industrial world. The flexibility of ctrlX I/O hints at the solutions coming to the factory of the future where a digital roadmap links individual machines to complete systems and on to the machine operators.
Bosch Rexroth continues to innovate in the automation, motion control and linear motion markets.
With the new Smart MechatroniX solution platform, Bosch Rexroth offers a combination of its linear motion technology components with electronics and software. These solutions can be used in a variety of areas including commissioning and processing and they can shorten the time-to-market. Modular systems are designed to be retrofitted, giving shop floor personnel a simple way to implement new technologies with legacy equipment already in use in the manufacturing facility.
The Smart Function Kit offers quick and intuitive commissioning and configuration for a range of processes, such as joining, pressing and handling. It works according to the plug and produce principle by combining preselected mechanical and electronic components with software. This modular toolbox consists of an electromechanical cylinder, a force sensor, a motor, a servo drive and a motion controller, plus a software package that enables easy commissioning and operation as well as comprehensive process analysis.
Bosch Rexroth will continue to expand its product offerings for the factory of the future and create advanced manufacturing hardware, software and engineering technologies that deliver maximum speed and minimal complexity.
boschrexroth.com/en/us/
Yasakawa Expands Ease of Use and Controller Performance
Building on prior software updates, the highly efficient Yaskawa Smart Pendant v2.1 is well-suited for quick robotic implementation of basic assembly, injection molding, inspection, machine tending, material handling, and pick and place tasks.
Enabling previously unsupported functions, software v2.1 provides a built-in classic interface view. Ideal for more experienced robot operators, this option enables the end user to reset minor and major alarms or to edit Concurrent I/O with reduced programming downtime.
Smart Pendant is available for use with select Yaskawa Motoman YRC-controlled robots.
Expanding on the performance improvements and extension app capabilities introduced previously, Smart Pendant v2.1 capability further improves configuration and programming of third-party devices, including Yaskawa’s Smart Packager software development kit (SDK). This desktop tool enables third parties to combine multiple components into a single convenient file. Each file, known as a Yaskawa Installation Package (YIP), enables easier robot setup by automating processes typically outlined in a manual.
Various advances, such as YRC1000 controller software updates, multi-touch jogging, 3D viewer optimizations, basic concurrent job support, improved HC-series configuration and other INFORM usability improvements are also included.
Smart Pendant is available for use with select Yaskawa Motoman YRC-controlled robots. Soft Pendant software – a digital version of the YRC1000 pendant that can run on a Windows operating system – is also included.
Expanding Smart Pendant capability for handling tasks, the easy-to-use Yaskawa Smart Pattern extension enables quick development of jobs for repetitive handling tasks. Ideal for common tasks like stacking, unstacking, case packing, machine loading and unloading, this intuitive interface provides guided prompts for single part, grid (2D array), 3D grid (3D array) and stack patterns.
Prompts are provided to create two types of jobs. Pattern jobs define a specific pattern and robot movement for handling each part in the pattern. Supervisor jobs define which patterns should be used to pick and place parts, as well as the overall flow of the system, including basic I/O signals. Easily customizable, job editing is available to accommodate specific system requirements. A wide variety of grippers and end-of-arm tooling can be used.
Compatible with the YRC1000 and YRC1000 micro controllers, Smart Pattern is available as a complimentary download for use with HC-series and GP-series robots.
motoman.com
Siemens Reduces Product Development and Time-to-Market with SINUMERIK ONE
Siemens is expanding digital transformation in the machine tool industry with SINUMERIK ONE. The new controller works with software to create the machine controller and the associated digital twin from one engineering system and thus contributes to the seamless integration of hardware and software. The interaction between the virtual and the real-world benefits machine tool builders and CNC machine users.
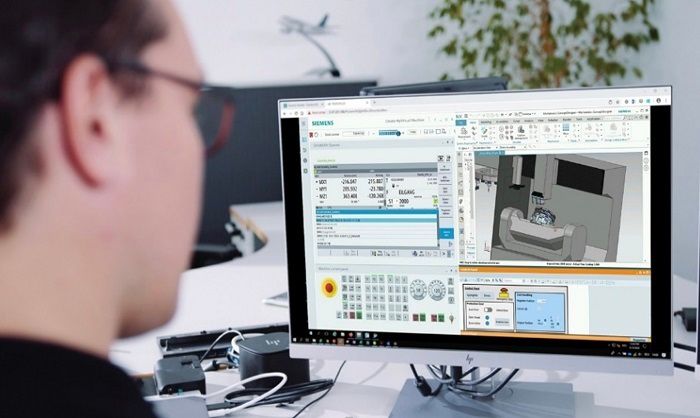
The CNC system with integrated Simatic S7-1500F PLC is available in both a control cabinet-based and panel-based version.
Machine tool builders can virtually map their entire development processes—significantly reducing the product development phase and time-to-market for new machines—with Create MyVirtual Machine. The virtual preparation of machine commissioning can also reduce the duration of actual commissioning considerably. Machine users can also benefit from a “digital first” strategy for their central processes during production when they use Run MyVirtual Machine. Programming, production planning and process optimization can be simulated instead of performing them directly at the machine and non-productive times are eliminated. Even training can be carried out using the digital twin instead of training on the actual machine.
The CNC system with integrated Simatic S7-1500F PLC is available in both a control cabinet-based and panel-based version. SINUMERIK ONE fits into the Totally Integrated Automation (TIA) Portal and makes a highly efficient engineering framework available for machine tool builders. With Safety Integrated, the new SINUMERIK ONE supports the consistent Siemens industry standard for safety. With IT security integrated in the CNC by design, SINUMERIK ONE implements the multi-layer Defense-in-Depth-Concept. Lear more here:
Usa.siemens.com/sinumerik-one
Heidenhain Offers Variety of Automation Innovations
PressFit rotary encoders from Heidenhain give small-motor manufacturers a better solution for incorporating automated mounting for feedback devices. This new ExI 11xx encoder series features a unique compact design that allows fast and simple mounting by press-fitting into a motor housing while still allowing surrounding space for cables and seals. Heidenhain’s PressFit encoders are made for integration into motors with a flange size as small as 40 mm x 40 mm or an axis height of only 20 mm.
Developed in collaboration with global motor manufacturers, Heidenhain’s new PressFit encoders include a “PressFit” flange that can be secured in a motor housing through a frictional connection, using a specially designed tolerance sleeve. This system promises to support automation efforts by easing mounting requirements, leading to less mounting time being required.
Press Fit encoders from Heidenhain.
From smart factories and robot builders to mobility companies and interstellar research, Heidenhain positioning control systems are helping shape the safe and productive future of unmanned operations. These components lead the market in positioning accuracy and dependability, ideal for unmanned or low-monitored mechanical designs. Technologies on display included everything from compact incremental solutions to heavy-duty absolute rotary encoders that withstand contaminants or shock.
heidenhain.us
Automate 2023 will take place May 22-25, 2023 in Detroit, Mich. at the Huntington Place Convention Center.
automateshow.com