Heat is also generated in an e-motor, sometimes quite a bit. In demanding applications, the motor electronics cause the power to be throttled or even shut down completely. But there is another clever way to protect an electric motor from overheating without losing power: using a thermally conductive casting resin as a heat transfer medium. The principle can also be called a static solid cooling system.
For the operator of an electric motor, it is always desirable if the thermo-technically critical operating point is far away, so that a reduction in power - or shutdown - is not even necessary. Uwe Köhler was already thinking about this in the 1990s and began developing thermally conductive casting resins. In the meantime, he has created Lambdapox, a product that offers a thermal conductivity λ = 8 W/m*K - a maximum value, but not a must. In the future, sales and customer support for the innovative product will be handled by the start-up "Lambda Resins" in Kerpen (Germany), which was founded specifically for this purpose. Lambda Resins is a joint venture between the inventor of Lambdapox and the Nagel Group from Nürtingen, Germany, which has production lines for electric motor stators in its portfolio through its group company Gehring Technologies.
So, what does Lambdapox do? The resin is capable of thermally stabilizing e-motors and thus enabling continuous operations at a high level, reliably, effectively and without a great technical effort. To achieve this, the stator winding of the motor is cast with the resin in a vacuum process. The effect is that the heat flows into the surrounding cooling jacket much faster than without this encapsulation. The problem of heat build-up in the winding is avoided. An alternative to this approach is forced cooling with oil. However, systems based on this approach have the disadvantage of higher technical complexity or the risk of oil leaks.
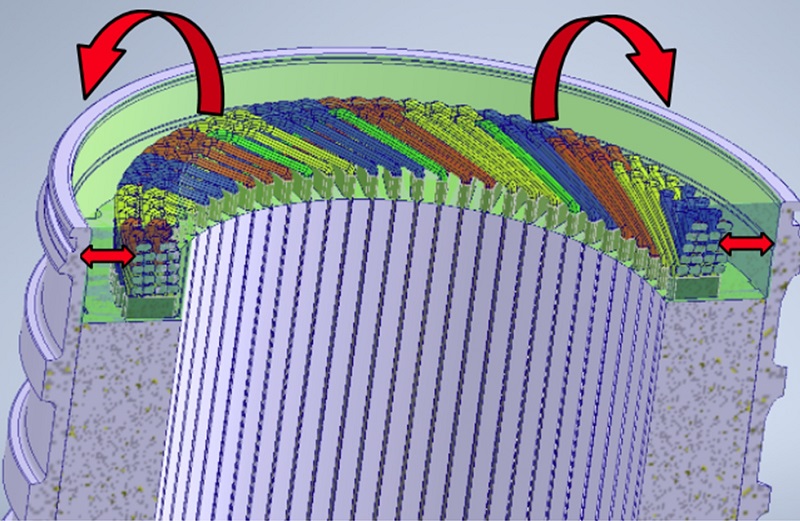
Each application has its own framework conditions. Therefore, Lambda Resins always tailors the casting resin to the customer's needs. For example, the thermal conductivity is variable - λ values in the range of 2.0 to 8 W/m*K are basically possible. Another variable is the insulation class according to DIN EN 60085 - the realization of insulation class H up to 180 degrees Celsius is standard. Lambdapox easily withstands the heat shock test from minus 40 to over 180 degrees Celsius. The cracking often observed in potting materials in the past during these tests is completely foreign to this resin. "Our casting resin causes a reduction in temperatures in the winding head of up to 40-60 degrees Celsius at the same load," said Köhler, highlighting the advantages. "Depending on the configuration, the motors achieve up to 50 percent higher continuous power at the same thermal load."
The cast resin is suitable for all high-performance motors, e.g., in the production industry, but especially also in e-vehicles. The focus can be either to maximize performance, or to minimize space requirements while keeping performance unchanged. The former enables performance-enhanced variants of an existing engine without the need for a new development. The latter leads to a less expensive unit and also to a lower CO2 footprint per kW of engine power.
The field of e-mobility, in particular, benefits from the use of cast resin. Lower engine heating results in higher efficiency or lower energy requirements. In the end, the range of the vehicle is increased.
"We first discuss the customer's design with them and then plan how the potting will be carried out. Then we create prototypes and check the performance on the test bench. The entire process from inquiry to test bench usually takes a few weeks to a maximum of about three months," said Köhler.
Demand for the innovative potting technology is already very high. The reason is obvious: high efficiencies, optimised sizes, fast implementation and low costs both for acquisition and operation, are absolute trend topics. This applies equally to mobile and stationary motors.